Cranfield University Collaboration
We recently had the opportunity to collaborate with the experts at Cranfield University to run a series of tests and simulations on one of our newest engineering designs – the SoloJet Air Nozzle (used in our Truck Blow-Off System (TBOS)), to see how well it performs under a range of conditions.
Solvair’s SoloJet Air Nozzles have been designed to sweep large surface areas and to remove 99%+ of plastic debris. Nozzle performance has to therefore remain consistent, and as TBOS is a system built for use in outdoor situations, this meant that the impact of weather, temperature change and other environmental variants were considered as part of the original design process.
Working with Cranfield University gave us the opportunity therefore to run scenarios and tests for the SoloJet air nozzle across a range of configurations. We were able to observe performance across different conditions, noting strengths as well as areas for improvement.
Why Cranfield University?
Cranfield University are one of the leading specialist postgraduate universities in the world that focus on business and engineering. They ranked 5th in the UK for mechanical, aeronautical and manufacturing engineering in 2019 (QS World University Rankings), and over half of all aerospace engineering Master’s students in the UK study at Cranfield each year.
We worked with Cranfield’s Centre for Propulsion Engineering. The Centre runs one of the largest MSc degree courses relating to propulsion and power systems, are renowned for their industrial projects, and their staff and students have received numerous international awards, including the ASME Aircraft Engine Technology Award, Alstom Golden Blade Award and ASME Student Awards.
As Air Flow Systems experts, SolvAir design, build and install Air Knife Systems for “precision drying”, including coating control, air curtains, removing dust and unwanted materials, as well as many other valuable applications. We benefit from having our own manufacturing facility allowing us to keep stringent checks on both productivity and ultimately, product quality.
The opportunity to work with Cranfield’s Centre for Propulsion Engineering gave us the opportunity to access some of the most innovative engineering technology in the world. The Centre has world-class, large-scale facilities to facilitate innovative modelling and testing, meaning systems can be examined and refined without the need for building actual models, which is a time and money intensive process.
Why test SoloJet Air Nozzles?
SolvAir’s unique SoloJet Air Nozzles are designed for blow-off in a range of Air Knife Systems. They form a key component of the new Truck Blow-Off System (TBOS) system, where they are optimally designed and positioned to target all areas of a truck’s surface where plastic spillage gathers, including wheel arches.
To achieve high velocity air stream needed in TBOS to remove all plastic debris the relationship between the blower pressure, manifold air distribution and force at the impingement region had to be considered. As well as this, the air mass flow rate, diameter of the nozzle, spacing between ports and the distance to the product surface are key variables.
We therefore used the technology at Cranfield to study single and multiple SoloJet Air Nozzle configurations under a range of industrial operating conditions, including the manifold interior.
The specific aims going into the testing were identified as follows:
- Visualise the discharge air pattern of the SoloJet Air Nozzle to better understand the application range.
- Quantify the mass flow rates for the SoloJet Air Nozzle under a range of operating conditions.
- Understand and quantify any air entrained in the jet from the surrounding medium.
- Visualise flow patterns with multiple SoloJet Air Nozzles in parallel on a single manifold.
- Visualise and characterise the flow within the manifold and nozzle interior.
- Note any obvious inefficiencies in the SoloJet Air Nozzle design and areas for improvement.
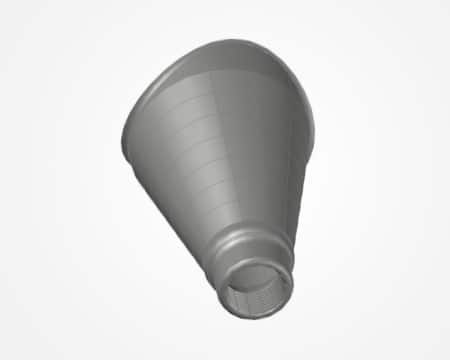
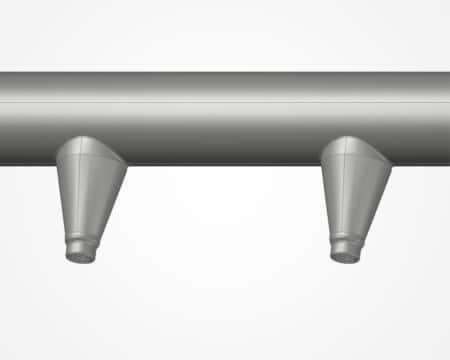
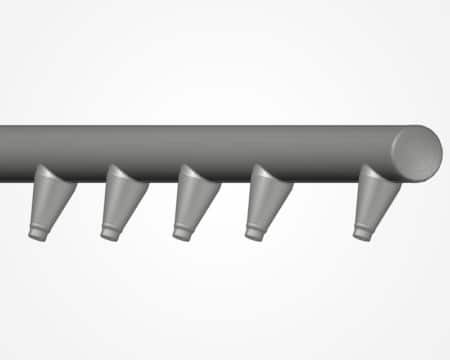
What is TBOS?
TBOS is the latest addition to our range of Air Knife systems. TBOS was designed as a part of SolvAir’s commitment to Operation Clean Sweep (OCS) as a way to easily help businesses minimise plastics escaping into the environment, without significant cost in time, money or business disruption to their organisation.
TBOS is an Air Knife blow-off system that uses SolvAir’s SoloJet Air Nozzles to direct high-velocity air streams at a truck’s surface, removing all pellets/nurdles, depositing them onto the floor area where they can be easily collected.
- Meets environmental responsibilities, including those set out in Operation Clean Sweep® (OCS).
- Easy to install and run, designed to result in no disruption to business or on-site operations.
- Fully automatic, energy-saving, and requires no additional resources such as water or manpower.
See our TBOS website for more details.

What is OCS?
SolvAir are signatories to Operation Clean Sweep (OCS), a global initiative set up to significantly reduce plastic pollution in the environment. Mismanaged industrial waste is one the greatest culprits contributing to plastic pollution. For example, the plastic pellets and nurdles coming from the plastic supply chain and being disposed of during the logistics process, have been identified as a significant pollutant.
Following OCS guidance, SolvAir identified that using blow-off installations to clean trucks carrying plastic resins could help seriously tackle plastic pellets/nurdles becoming pollutants. However, this also required a completely bespoke system, with unique nozzle design and layout, to make this possible.
What did we do?
Our team collaborated with Cranfield University to investigate the flow characterisation of the SoloJet Air Nozzle design under a range of different operating pressures. A summary of methods used is set out below.
Computational Fluid Dynamics (CFD)
We used Computational Fluid Dynamics (CFD) – a tool that simulates the flow of physics with a high-level accuracy – to ensure that the force required in a system could be facilitated by our design. Using CFD means that we could test the SoloJet Air Nozzles under a range of conditions, without the need for building prototypes, resulting in savings in both time and money.
We used CFD to first stage two-dimensional simulations of the airflow so we could make sure the velocity and mass flow profile was optimised in each port. We then used this data to stage three dimensional simulations of the whole system. Underpinning our final calculations was an analytical formulation that took into account reasonable assumptions, and was compared against the velocity profiles of the CFD simulations. It showed that a great level of agreement was present in relation to the assumptions required by the problem, meaning the system was highly likely to perform excellently.
Manifold Flow Characteristics
A dividing-flow with five ports and specified geometry was investigated. The Reynolds Average Navier–Stokes (RANS) approach, Reynolds Stress Tensors and the Shear-Stress Transport models were applied.
In terms of internal manifold flow, a number of inlet pressure conditions were carried out in order to assess how the manifold distribution behaves at low, medium and high pressure.
CFD simulations carried out in this work were conceived to provide quantitative support to understand the physics of the Truck Blow-off Station (TBOS) system and propose optimisation procedures.
Two-Dimensional SoloJet Study
To assess the overall jet characteristics and quantify the level of jet entrainment (if any) a compu-tational set-up capable of replicating realistic flow physics was established. This included two preliminary studies designed to test the implications of the computational domain size and discretisation properties (resolution) of the domain.
Manifold with impinging flow
The simulation of the coupled system was then carried out taking into account the experience of the computational domain size and grid refinement from the previous segregated cases.
Results
As a result of the two and three dimensional CFD simulations, the SoloJet Air Nozzles were shown to perform to a consistently high standard. This meant that no potential improvements, or points of failure, were identified.
In addition, the following conclusions were made:
- CFD simulations demonstrate an equally distributed mass flow between each manifold port.
- Comparisons with a non-constricted case gives strong evidence that the sharp angle and high diameter ratio between the port and Solojet exit gives additional pressure loss.
- High pressure regions are found between the manifold and SoloJet Air Nozzle entrance.
- A recirculation region is formed between the parallel jets and impinging wall.
Jet entrainment is found that reaches a maximum at approximately 11D from the nozzle exit. - For multiple impinging jets, the mixture occurs after 10D from the nozzle exit.
- Jet morphology and dynamics remain consistent across all operating conditions tested.
“Working with Cranfield University’s Centre for Propulsion Engineering was a fantastic opportunity to have our Air Knife Systems examined by experts. Our internal knowledge, systems, processes and products are world class, and that our latest Air Knife system excelled in state of the art testing facilities, confirmed by this study, is a great credit to our team”.
Chris Davies | SolvAir CEO
Free Consultation
To discuss how our SoloJet or SV10 Air Nozzles can impact your business, please call us on +44(0) 1473 320 307, email us at info@solvair.co.uk, or contact us now and one of our team will be in touch within 24 hours.