Energy Savings
Our blower powered systems often demonstrate significant energy savings over alternative solutions using compressed air, heating and manual intervention.
Why do factories use compressed air for open blowing applications such as drying and cleaning products?
Compressed air is often the first solution because the air supply already exists in the factories and it can be applied to the line at a very small cost. Nozzles and pipework are low priced items. The ongoing energy costs to operate the solution are overlooked or not understood by the engineers.
The scenario is almost always the same, the plant engineer has a process issue which can be resolved by the introduction of air. He is under pressure to resolve the issue as soon as possible and he identifies an existing supply of compressed air from the facilities network. He can use this supply or air and discharge it onto the process through DIY devices such as open ended pipes, flattened pipes, pipes with a series of holes drilled into them and the list goes on. Or maybe he purchases some low cost designed solutions such as fan or cone nozzles. Whichever way he resolves the task he in most cases finds a relatively quick solution using existing resources and costing very little to implement.
But, what has not been considered is the ongoing costs to operate this solution!
Why are Blowers more energy efficient than compressed air?
Think about it – here we have air being released to atmospheric pressure which has undergone the compression process from 0 to 6 bar and above in the facilities compressed air system. Is this an efficient use of energy?
Going back to the original process what was needed to solve the issue was typically a high flow of air at a good impact velocity. A system that could provide this would need to generate the pressure required to deliver the air from generation to discharge but much lower than 6 bar. Blower systems generate pressures upto 0.25 Bar however the majority of applications only need a system pressure of around 0.15 Bar (150mbar).
And this is the significant difference between the industry standard solutions of compressed air versus specifically designed blower systems.
Can Blowers & Air Knives really perform as well as compressed air nozzles?
In the vast majority of applications they can. Generally blower systems work at much higher flow rates than compressed air systems which means they often outperform them.
Blower driven systems can generate air knife outlet velocities upto Mach 0.6 = 454 mph = 731 kph = 40,000 fpm = 203 m/sec. This speed combined with high volume flow rate breaks the mechanical bond between the liquid and the surface, lifting the droplets off the product.
How to assess your compressed air consumption
An easy method for checking your system yourself is to assess the volume of air used in cubic metres. You can then use the calculation 1m³ = 0.11 kW. How we get to this is detailed in the next section “Costs of Compressed Air Production”.
If you are using a dedicated type of air nozzle/device you should be able to locate the technical information for the product online. Here you will learn the amount of flow/volume the device consumes at varying pressures.
If you are using a more basic open pipe solution then again look online. You will find many sites that publish data on “compressed air through open pipes”.
If you need any help then contact SolvAir, we would be happy to help.
Costs of compressed air production
From small to large compressors the cost of producing each cubic metre of compressed air is similar. If you know the maximum capacity of your compressor in m³/hr and the power consumption in kW then you can calculate how much it costs to produce ONE m³ of compressed air.Opposite are examples using data taken from the data sheets of a Leading Compressor Manufacturer:
Small | Medium | Large | ||
---|---|---|---|---|
Conclusion = Each Cubic Metre (m³) of Air used from a compressed air system consumes 0.11 kWh (kilowatt hours) electrical energy. | ||||
A |
Inlet Capacity m³/min
|
6.31 | 11.6 | 42.3 |
B |
Converted to m³/hour (A x 60)
|
378.6 | 696 | 2538 |
C |
Compressor Power kW
|
42.6 | 79.3 | 271.9 |
Power (C) ÷ Air Capacity (B) = kW per m³/hour
|
0.1125 | 0.1139 | 0.1071 |
Key facts and guidance in relation to compressed air use.
Costly Compressed Air – Although one of the most expensive forms of plant energy, compressed air is easily accessible, and simple to adapt for use. Consequently it is commonly used for applications where other energy technologies and energy inputs would be more efficient and economical.
“Of the total energy supplied to a compressor, as little as 8-10% may be converted into useful energy that can do work at the point of use. This makes it a very expensive for of energy” – Carbon Trust
“Program to eliminate any inappropriate uses of compressed air” – British Compressed Air Society
“The kWh price of compressed air is ten times greater than the price of electricity so it makes sense to identify areas where compressed air could be replaced with a less energy intensive alternative” – Carbon Trust
“Compressed air is generated using electricity. Moreover, the fact is that its generation is equivalent to about 10% of industry’s total electricity usage, rising to 30% in some sectors, highlights why companies have compelling reasons to investigate the potential for energy saving in this area” – Leading Manufacturer of Motor Control and Power Conversion Technologies
Air Knife Systems VRS Heated Air Systems / Ovens / Heat Tunnels
Heated systems rely on evaporation to dry the products. These are often on relatively slow speed production lines which provide sufficient time for the product to be exposed to the heat whilst passing through a contained area like a heat tunnel. Sometimes the drying of a product needs to go beneath the exposed surface and this is typically where heat is used.
However sometimes air knives can be used in combination with a heat tunnel, used as a pre-drying stage to blow-off a high percentage of the water prior to the heated system. Sometimes allowing for the temperature in the heated section to be reduced saving energy and money.
Compressed air CAN sometimes be the best solution.
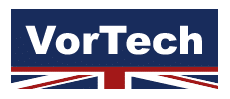
If your requirement for blowing is intermittent then compressed air can a good solution because it is more controllable than a blower system. For example, if your process only needs a 5 second blow-off every minute, compressed air can be used with a solenoid valve to start/stop the supply. This simple modification to an existing system means that the compressed air consumption is kept to a bear minimum. In this situation a blower system is not likely to demonstrate a reasonable return on investment. If this sounds like your scenario then visit www.vortextube.co.uk
Comparing the useful output of a Blower powered system VRS Compressed Air.
Lets Compare…
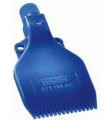
A typical FAN NOZZLE (40-50mm wide) regularly seen in operation across manufacturing sites consumes:
- 50.7 m³/hr at an operating pressure of 7.0 bar
- 0.1 kW compressor power = 1.0m³ compressed air
- 50.7 m³/hr x 0.1 kW = 5.07 kWh (Kilowatt hours)
Our blower range includes models starting at 2.2KW through to 15kW. Across this range we average a typical output of 180mm width per kW power consumed.Using the equivalent power consumed by a SINGLE FAN NOZZLE 5.07 kW, which provides an airstream across 40-50mm, our blower systems could support and airstream in excess of 900mm width.
Opposite are examples using data taken from the data sheets of a Leading Compressor Manufacturer:
Slot Coverage | Round Nozzles | ||||||
---|---|---|---|---|---|---|---|
Per KW | COMPRESSOR (based on fan nozzles @ 7 bar) mm Width |
BLOWER (Air Knife) mm Width |
DIFFERENCE | COMPRESSOR (No. of 2mm Ø nozzles @ 6 bar) |
BLOWER (No. of 10mm Ø nozzles) |
||
1 | 10 | 180 | 170 | 0.64 | 2.25 | ||
2 | 20 | 360 | 340 | 1.28 | 4.5 | ||
3 | 30 | 540 | 510 | 1.92 | 6.75 | ||
4 | 40 | 720 | 680 | 2.56 | 9 | ||
5 | 50 | 900 | 850 | 3.2 | 11.25 | ||
6 | 60 | 1080 | 1020 | 3.84 | 13.5 | ||
7 | 70 | 1260 | 1190 | 4.48 | 15.75 | ||
8 | 80 | 1440 | 1360 | 5.12 | 18 | ||
9 | 90 | 1620 | 1530 | 5.76 | 20.25 | ||
10 | 100 | 1800 | 1700 | 6.4 | 22.5 | ||
11 | 110 | 1980 | 1870 | 7.04 | 24.75 | ||
12 | 120 | 2160 | 2040 | 7.68 | 27 | ||
13 | 130 | 2340 | 2210 | 8.32 | 29.25 | ||
14 | 140 | 2520 | 2380 | 8.96 | 31.5 | ||
15 | 150 | 2700 | 2550 | 9.6 | 33.75 |
SolvAir Offers Free Site Surveys
Contact our office if you would like us to arrange an engineer visit to review your current compressed air open blowing applications. We will impartially advise if our blower systems could offer you energy savings and an attractive return on investment.